Rotational molding is a manufacturing process that creates hollow plastic products by heating and rotating a mold along two axes. Adjusting rotational speed is crucial because different resin types behave differently at various speeds. The right speed ensures consistent wall thickness, smooth surfaces, and optimal product strength. Speed control directly influences the quality and consistency of molded products, making it essential for achieving the best results. In this blog, we will explore how to adjust rotational speed for different resin types in rotomolding.
Understanding Rotational Speed in Rotomolding
In rotational molding, rotational speed refers to the rate at which the mold spins along two perpendicular axes. The speed at which the mold rotates is essential for ensuring that the resin is evenly distributed throughout the mold, significantly impacting the final product quality.
Two-Axis Rotation
- Uniform heating and cooling: The mold rotates on two axes, helping distribute the resin evenly.
- Faster speed: Can speed up heating but may lead to uneven resin distribution.
- Slower speed: Allows for better control of melting but may extend cooling time.
Key Factors Affected by Rotational Speed
- Wall Thickness: Faster speeds typically result in thinner walls, while slower speeds can create thicker walls.
- Uniformity: Maintaining consistent speed helps ensure uniform wall thickness and a stronger structure.
- Surface Finish: Proper speed adjustment leads to smoother surfaces, minimizing defects like air bubbles or rough textures.
How Resin Type Affects Rotational Speed in Molding?
Different resin materials used in rotational molding each have distinct properties that influence their behavior at various rotational speeds. By adjusting the speed according to resin type, manufacturers can optimize product characteristics such as strength, flexibility, and surface finish.
1. Polyethylene (PE)
- Speed Behavior: Polyethylene is widely used in rotational molding due to its ease of melting and low viscosity. This allows the resin to flow smoothly when heated.
- Ideal Speed Adjustments: For PE, moderate rotational speeds work best. Faster speeds may cause uneven resin distribution, while slower speeds help ensure a uniform layer.
- Impact on Product: When the speed is adjusted correctly, PE creates strong, lightweight products with smooth surfaces. Too high a speed can result in thinner walls, which may compromise product strength.
2. Polypropylene (PP)
- Speed Behavior: Polypropylene has a higher melting point and viscosity compared to polyethylene, meaning it requires more precise control over the rotational speed.
- Ideal Speed Adjustments: Slower rotational speeds are necessary to ensure even melting and resin flow for PP. This ensures better resin distribution and results in thicker, stronger walls.
- Impact on Product: PP’s chemical resistance and durability make it ideal for products exposed to harsh environments. Proper speed adjustments not only ensure strength but also maintain flexibility and resistance to impact.
3. Polyvinyl Chloride (PVC)
- Speed Behavior: PVC has a lower flow rate than PE and PP and tends to cool faster, making it more challenging to mold at higher speeds.
- Ideal Speed Adjustments: To achieve optimal results, a slower speed is required to ensure proper heating and prevent premature cooling, which can cause uneven molding.
- Impact on Product: PVC is perfect for applications that demand high strength and chemical resistance. Adjusting the speed correctly helps achieve smooth surfaces and durable products. If the speed is too fast, the result may be inconsistent wall thickness or a rough texture.
Key Considerations for Each Resin:
- Strength vs. Flexibility: Speed adjustments help balance strength and flexibility. Faster speeds create thinner, more rigid walls, while slower speeds produce thicker, more flexible walls.
- Surface Finish: Speed adjustments also influence surface quality. Faster speeds may cause rough textures or air bubbles, while slower speeds help ensure a smooth, even finish.
Adjusting Speed for Different Resins
Adjusting rotational speed based on resin type is key to achieving the best quality in your molded products. Each resin type behaves differently, requiring tailored speed settings for optimal results. Below are guidelines for adjusting speed for commonly used resins in rotational molding.
1. Polyethylene (PE): Ideal Speed and Tips for Consistency
Ideal Speed: Polyethylene is a popular resin for rotational molding, known for its low viscosity and ease of melting. For PE, moderate rotational speeds of around 5-10 RPM work best, depending on part size and mold design.
Tips for Consistency:
- Start with a moderate speed to ensure even resin distribution. Adjust if necessary.
- Avoid high speeds, which can lead to uneven resin flow and thinner walls, compromising strength.
- Maintain a uniform mold temperature throughout the cycle to ensure a smooth surface finish.
2. Polypropylene (PP): Adjustments for Higher Melting Points
Ideal Speed: With its higher melting point and viscosity, polypropylene requires slower rotational speeds—typically between 3-5 RPM—to ensure even resin flow and heat distribution.
Adjustments:
- Slower speeds help to ensure thorough melting and create thicker, stronger walls.
- Slow speeds reduce the risk of premature cooling, which could lead to uneven molding.
- Higher mold temperatures can help manage the material's slow flow during the molding process.
3. PVC and Other Materials: Speed Adjustments for Various Resins
Polyvinyl Chloride (PVC): PVC requires slower rotational speeds (typically 2-4 RPM) as it cools faster than PE or PP. Slower speeds ensure that the resin stays molten long enough to properly coat the mold.
Tips for PVC:
Slow down the rotational speed to avoid rapid cooling, which can cause uneven finishes or incomplete molds.
Ensure the mold temperature is high enough to maintain the resin's flow and consistency.
Testing and Fine-tuning Rotational Speed
Achieving the ideal rotational speed is essential for producing high-quality molded products. Fine-tuning the speed through testing ensures optimal results, ensuring that the resin flows properly and the mold is filled evenly. Here's how to approach it:
- Trial Runs: Test different rotational speeds for each resin and part size to understand how they react. This helps ensure uniform wall thickness and smooth surface finishes.
- Machine Calibration: Regular calibration ensures that the machine runs at the correct speed settings, preventing errors and ensuring each cycle is consistent with production goals.
- Monitor During Production: Keep an eye on resin flow, temperature, and mold conditions during production. Make any adjustments needed to maintain consistent quality and avoid defects.
Resin Behavior and Rotational Speed Table
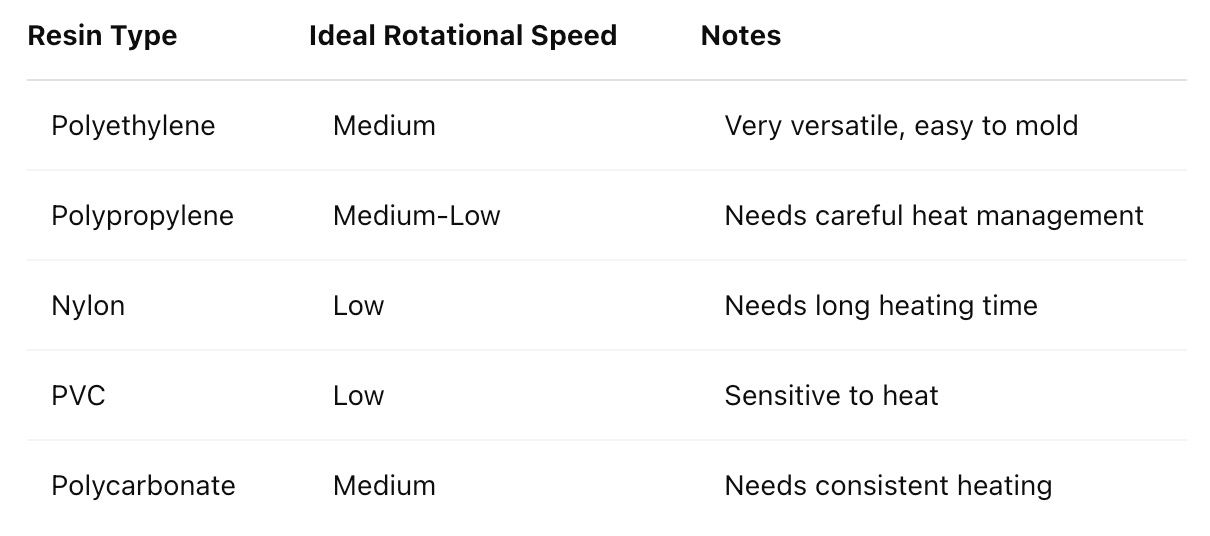
Common Issues with Speed Adjustments
Adjusting rotational speed can sometimes cause issues that affect the final product. Here's how to identify and solve the most common problems:
- Overheating: Speeding up too much can cause overheating, leading to premature resin curing.
- Solution: Lower the speed or allow more time for cooling to help the resin distribute evenly.
- Uneven Wall Thickness: Incorrect speed can cause inconsistent wall thickness, impacting the strength of the product.
- Solution: Test different speeds to achieve uniform wall thickness throughout the product.
- Air Bubbles and Defects: Faster speeds may lead to air bubbles or surface imperfections due to uneven resin distribution.
- Solution: Reduce speed to ensure proper resin flow and check mold temperature to prevent rapid cooling.
Best Practices for Adjusting Speed
To achieve consistent, high-quality results in your molding process, it's essential to follow these best practices:
- Adjust Gradually: Make small adjustments to the rotational speed to avoid overshooting the optimal setting.
- Maintain Consistent Temperature and Speed: Keeping both the speed and temperature steady is crucial for uniform results. Avoid any sudden fluctuations during production.
- Monitor Each Cycle: Continuously monitor the molding cycle to ensure the speed remains steady and the resin is distributed correctly. This minimizes issues like uneven wall thickness.
- Keep the Machine in Top Condition: Regularly calibrate and maintain your molding machine for accurate and efficient production.
Conclusion
Adjusting rotational speed for different resin types is essential for achieving consistent, high-quality products in rotational molding. By understanding the unique behaviors of resins like PE, PP, and PVC, manufacturers can fine-tune their processes for optimal strength, flexibility, and surface finish. Regular testing, machine calibration, and monitoring are key to maintaining precision. For those looking to enhance their molding efficiency, Benfan Machine offers advanced solutions to optimize production.